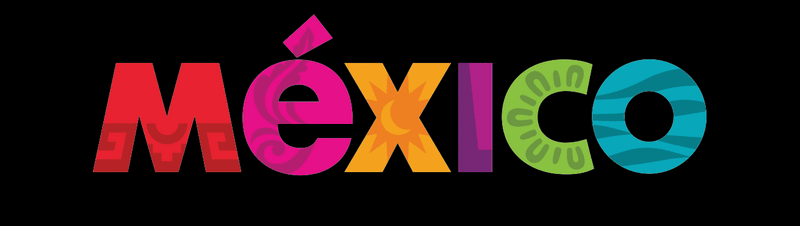
- Urgently required for renowned Offshore / Onshore Oil & Gas Company in Worldwide.
LOCATION : MEXICO
Maintenance Superintendents (AG - 606)
Qualification & Experience:
-Degree / Diploma in Engineering with minimum 10 to 20 years experience in relevant field.
-Spanish and English language.
-Profiles with production experience in FPSO.
-Good experience as Supervisor / Superintendent.
Mission:
-Ensure safe maintenance execution in compliance with HSE rules, legislative regulations and international std. and ensure the implementation of an efficient Maintenance Plan maximizing up-time and ensuring appropriate reporting.
-Lead a multi-discipline team (including discipline Supervisors and discipline Technical roles).
-Ensure that company policy and Project Service Contract Technical SOW are cascaded, and targets are achieved.
Tasks:
Maintenance Execution
-Interface with Maintenance Site Report for all Technical Issues
-Support Maintenance Site Report on monthly and annual planning
-Cooperate with the planning team and assign the daily activity to the discipline Maintenance Supervisors
-Ensure discipline to the Permit to Work system
-Coordinate the maintenance operations
-Check and validate technical reports-
Prepare maintenance reports to Maintenance Site Report.
-Report on the progress of maintenance operations and execute performance monitoring (KPI)
-Analyse the activity and, if necessary, propose improvements
-Participate to daily, weekly and site co-ordination meetings
Technical Support / Methods
-Ensure the operating and maintenance procedures and tools used by his crews are appropriate and, if necessary, suggest improvements to the Contractor Site Representative
-Ensure co-ordination between maintenance operations and planning/Preparation CMMS team
-Keep record of work that can be performed only during inspections or shutdowns
-Promote and propose modifications and improvements
-Suggest corrective measures to the Maintenance Site Repot or Client if the backlog trend increases
-Anticipate potential problems that could occur in the production plant, in close relationship with other sections, in order to prevent non-productive or non efficient operations
-Create a sound and professional relationship with Client reps., team and subcontr.
Team Management
-Be responsible for his teams on in local site (offshore/onshore)
-Ensure the correct behaviour of his teams in accordance with the general safety regulations of the Company and, if needed, take the necessary corrective measures
-With the assistance of Contractor support functions and Maintenance Site Repair., validate the crew change schedule (admin, logistics, etc)
-Actively involved (and lead when no CSR/MS) with the Competence Assurance System, including proposal of the annual appraisals, train the trainer programs, coaching
-Develop continuously his team members, identify the training needs. Check the validity of mandatory individual certifications and qualifications
-Manage Nationalization and succession plan and propose adjustments and improvements HSE
-Ensure that the team has the necessary competencies for safe execution of the assigned work
-Promote understanding of workplace hazards and levels of risk, and encourage awareness in individuals of their valuable contribution to the elimination/mitigation of risk Promote HSE culture via strong safety leadership, ensuring all activities are undertaken with full knowledge of Company commitment to health, safety and the environment
-Ensure all necessary controls to mitigate risks and/or eliminate hazards
-Execute performance monitoring via regular observation of working practices, assessing compliance with safe systems of work and work instructions.
Operation Superintendents (AG - 606)
- Qualification & Experience:
Degree / Diploma in Engineering with minimum 10 to 20 years experience in relevant field.
Mission:
Responsible for the safe, efficient and correct operation of the Production Plant, process, gas compression systems, machinery, equipment, Central Control Room (CCR) and process instrumentation on the FPSO.
Tasks:
General Tasks applicable during all phases:
-Operate the process plant safely and efficiently in line with corporate policies and procedures
-Promote/implement Company QHSE Policies
-Implement, maintain, review Company QHSE Man agement system
-Report/investigate Accident/Incident, Near Misses, unsafe acts/conditions, HSE Non Conformities and other issues with safety impacts
-Carry out assigned duties during an emergency situation, as detailed in the Emergency Response Procedures
-Have knowledge of Permit to Work System and act as Area Authority for process plant
-Be fully conversant with Isolation Philosophy, Risk Assessment, Job Safety Analysis requirements
During Operations Phase:
-Report to FPSO OIM Master
-Ensure correct personnel training for production department
-Assess competence of the Production personnel
-Manage day-to-day disciplinary/performance issues on board for Production dept. in conjunction with OIM
-Prepare/implement/controls process procedures in line with safety standards
-Maintain close working relationships with all the Superintendents/Supervisors
-Plan/anticipate spare parts, consumables, chemical and other material requirements together with other Superintendents
-Ensure that planned maintenance requirements are undertaken in accordance with manufacturers recommendations/operating experience in a timely manner (PMS computerized system)
-Prepare/follow up/close out vendor assistance in production systems on board with OIM and FPSO Operations Manager
-Be responsible for all matters related to laboratory testing/analysis and direct the Laboratory technicians.
-Liaise with Client with regard to safe and optimal operations of process plant
-Ensure that comprehensive logs are maintained for Process Plant. Audit regularly production dept. registers/records.
-Administer/monitor a Code of Safe Handling of Hazardous substances on the FPSO and maintain product data sheets on file
During Pre-Operations Phase:
-Ensure that all refurbishment/conversion works to the Production Systems are of a standard suitable for the design life with uninterrupted service. This should include workmanship, materials, operability and Class requirements
-Ensure that all commissioning activities are performed in compliance with agreed plans and that, for each system, the appropriate acceptance documents (e.g. completion check lists, test reports, start-up reports, hand-over protocols) are signed off by authorized personnel
-Assure that Production Personnel are properly trained, define/implement relevant training plan
-Prepare/follow-up punch list items to ensure work completion
-Assist the Maintenance Dept. in Planned Maintenance Database data entry
Apply Online: www.asiapower.in/jobs
- Email: chennai@asiapower.co, delhi@asiapower.co, kochi@asiapowerltd.com, vad@asiapowerltd.com
No comments:
Post a Comment
Please give your feedback or Job Request here